Réalisation du forage pour essais pressiométriques par un système de tube fendu auto-fore (STAF)
Gérard ARSONNET, Geomatech, Champlan – France
Jean-Pierre BAUD, Eurogeo, Avrainville – France
Michel GAMBIN, Apageo, Magny les Hameaux – France
Résumé
Dans la continuité des recherches et mises au point de Louis Ménard, plusieurs de ses collaborateurs, associés avec de plus jeunes géotechniciens ont cherché un moyen de réaliser la cavité où doit être introduite la sonde pressiométrique en mettant en jeu les techniques de forage les plus récentes, la procédure restant globalement économique. La cavité proposée est quasiment exempte de remaniement et le sol avoisinant exempt de relaxation. Des exemples comparatifs sont fournis dans un grand nombre de sols.
Introduction
Dès les débuts de l’utilisation du pressiomètre, Louis Ménard et ses premiers collaborateurs se sont trouvé confrontés aux critiques de géotechniciens sceptiques sur la représentativité des essais dans différents types de sols. Les premiers utilisateurs ont donc dû s’attacher à définir les conditions de forage et d’essai qui donnaient les résultats les plus fiables. Le rôle de la bonne tenue des parois du forage, et la possibilité de disposer d’une cavité cylindrique bien calibrée au diamètre de la sonde sont rapidement apparus comme essentiels (PLM, 1962) L’utilisation de la tarière à main, à faible profondeur, à sec dans des terrains à dominante argileuse au-dessus de la nappe, ou avec circulation de bentonite, est ainsi devenu l’archétype de l’essai de qualité. La sonde pouvait être introduite peu de temps après le forage dans un trou aux parois bien découpées et lisses, dans lequel dès les premiers paliers le contact de la sonde avec le terrain était obtenu sans trace de remaniement (LCPC 1971). Les machines de forage géotechniques des années 60 étaient principalement à transmissions mécaniques et construites pour le sondage carotté. Louis Ménard et ses collaborateurs ont dans un premier temps produit des sondes pressiométriques de diamètres adaptés aux carottiers de 3’’, 3½’’, 4’’, 4½’’ et même plus. Les temps de manipulation et de mise en place de la sonde étaient trop longs et favorisaient la décompression des terrains excavés avec les outils de type carottier. On s’est ainsi assez vite orienté vers des sondes de plus petits diamètres, 32mm (1¼’’), 44mm (1¾’’), 63mm (2½’’), permettant la mise en œuvre dans des forages à la tarière à main, ou par battage d’un carottier. Très tôt, Louis Ménard (1959) brevetait le tube fendu destiné au battage direct de la sonde dans les sols granulaires sous la nappe, dont les parois des cavités sont difficiles à maintenir sans éboulement. Des machines hydrauliques de vibro-battage étaient également conçues et produites pour mettre en œuvre ce tube fendu, essentiellement en milieu marin (Ménard et Gambin, 1965). Car un deuxième problème était et reste crucial, celui relatif aux temps morts associés à la réalisation des essais d’une « passe autorisée » selon la norme : le temps passé à remonter l’outil de forage après chaque passe, puis celui passé à descendre la sonde pour réaliser l’essai enfin celui à remonter la sonde et redescendre l’outil de forage. C’est dans le but de résoudre ces problèmes de temps mort que de nouvelles recherches sont lancées qui déboucheront sur le dépôt d’un brevet qui contient en germe le procédé que nous allons présenter (Ménard 1976). On y trouve en effet à la fois le concept de l’auto-forage d’un tube, ici par « rétro-jet », éventuellement associé à un battage au câble à l’aide d’un mouton élancé, coulissant dans la partie inférieure du tube et celui d’une sonde de pressiomètre placée à demeure au droit de la partie fendue selon plusieurs génératrices du tube (figure 1).
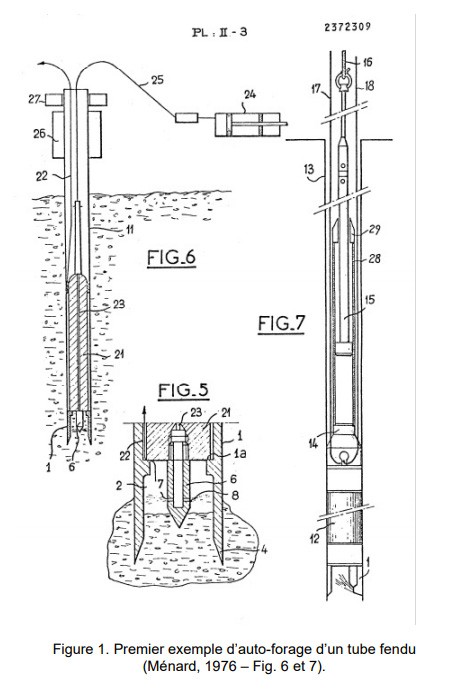
La méthode décrite dans le brevet permettait à la fois de s’affranchir de la notion de passe autorisée de forage, les parois du forage étant toujours maintenues tandis que les essais sont effectués lors de la remontée du tube et de supprimer les temps de manipulation de l’outil de forage. Toutefois, cette technique n’est applicable qu’aux sols meubles, à moins de disposer d’un équipement très haute pression de « jet-cutting » encore peu maniable sur les petits chantiers d’étude géotechnique.
Le tube fendu ou « lanterné »
Les méthodes de forage permettant de réaliser une cavité qui soit compatible avec la réalisation d’un essai pressiométrique fiable sont nombreuses, mais généralement associées à un type de sol bien défini (AFNOR, 2000). Parmi celles-ci revenons sur celles qui mettent en jeu un tube « fendu ». Le tube fendu - ou tube « lanterné », ce qui est plus explicite - dont la diversité des diamètres s’est raréfié pour privilégier le diamètre 63 mm (env. 2½’’), est actuellement utilisé de 3 façons dont le principe est radicalement différent : - Comme « tube fendu direct » : le tube fendu, fermé à son extrémité par une pointe (de préférence au bout d’un coupon de tube) ou un carottier est enfoncé directement, par battage, vibro-fonçage ou vérinage, une sonde pressiométrique de diamètre 44 mm étant fixée à l’intérieur ; c’est l’équivalent de l’outil de « forage » utilisé avant réalisation de l’essai, plus exactement l’outil de création de la cavité d’essai, la densification temporaire du sol au voisinage de la pointe étant ré-équilibrée par les vibrations postérieures dans les sables noyés au niveau des fentes du tube (TLM, 1966) ; la longueur des passes n’a pas de limite, celle du forage est limitée par le refus du battage. - En tant que tube lanterné (les anglo-saxons diront « Chinese lantern ») dans un forage réalisé au préalable : utilisé ainsi comme protection d’une sonde AX (44 mm) en lieu et place d’une sonde BX (60 mm), l’ensemble constitue une sonde utilisée dans un forage aux parois soit mal maintenues, soit partiellement maintenues par une colonne de boue de forage ; la résistance du tube à l’agressivité du sol des parois, généralement hétérogène, permet de réaliser un forage calibré plus « serré » que pour une sonde à gaine souple, la réduction de diamètre pouvant descendre à une valeur inférieure à celle de la sonde, ce qui conduit à la technique dite du trou pilote, intermédiaire entre un véritable forage préalable et l’utilisation d’un tube fendu direct ; la longueur des passes est limitée selon la norme en fonction du type de terrain testé. - Comme tube fendu « ouvert » opérant comme un carottier, les matériaux découpés étant enlevés soit postérieurement à chaque phase de battage de durée limitée en descendant un outil ad hoc, soit simultanément par buses rétro-jets permanentes à la base, la remontée des sédiments étant assurée par le flux injecté, ou par un outil rotatif destructif intérieur avec circulation de boue ; la longueur des passes n’a pas de limite, si ce n’est celle de la pénétration maximale sous l’effet des frottements sur le tube. La dernière technique, pourtant très attractive au point de vue concept, a été de moins en moins pratiquée, en raison d’une offre croissante de machines de forage multifonctions, au point de quasiment disparaître, bien que l’obligation de limite de longueur de passes imposée par la relaxation du sol y soit devenue sans objet. Disparue du tableau des méthodes entre le mode opératoire pressiométrique (LCPC, 1971) et la première publication de la norme française (AFNOR, 1991), elle est désignée dans la version actuelle (AFNOR, 2000) sous le nom de « tube fendu avec enlèvement simultané des matériaux » par l’acronyme TFEM. Cette technique est également décrite et autorisée dans la norme américaine (ASTM, 1987) au § 7.4.2.9 sous le titre « trou pilote et mise au calibre simultanée » (Pilot Hole Drilling and Simultaneous Shaving) : « forer avec un outil pilote de diamètre plus petit que la sonde et mettre au calibre la cavité à l’aide d’un cylindre creux mince situé juste au-dessus de l’outil et lié au train de tige. L’outil pilote et le tube sont poussés avec une circulation de boue épaisse ». Pouvait-on aller plus loin que ces descriptions et en augmentant sans limite la pénétration du tube, diminuer ainsi les temps de remontée et de re-descente de l’outil de forage, entre les périodes d’essais, inhérents au procédé ?
Auto-forage du tube fendu ou STAF
C’est sur la base de ces données que les auteurs de la présente communication se sont attachés à mettre un point une méthode de forage unique, quel que soit le type de sol, permettant la réalisation d’essais pressiométriques fiables, le remaniement des parois du forage étant réduit au strict minimum et restant quasiment le même quel que soit le sol. Nous avons ainsi cherché à optimiser les deux paramètres influant sur la forme du début de la courbe pressiométrique : - le « remaniement » des parois du forage proprement dit, en recherchant une technique de découpage du terrain rapide, unique et précis dans son calibrage, parfaitement cylindrique et assurant une évacuation rapide et complète des sédiments ; - la décompression du sol environnant, phénomène qui débute dès ce découpage effectué et quelle que soit sa qualité, en assurant le soutènement de la paroi du forage par un tube du calibre exact de la sonde en quelques fractions de seconde après le découpage du sol.
Le matériel
Le matériel nécessaire est choisi de façon à pouvoir être mis en œuvre par tout type de machine de forage hydraulique permettant la roto-percussion couplée à la circulation d’un fluide de forage. Il comporte, dans la version utilisée pour les résultats exposés au chapitre 4 ci-après, les éléments suivants :
- un raccord permettant de relier la sortie d’emmanchement de la tête de rotopercussion avec les tiges R32mm de type cordon, il est élargi pour appuyer sur un casque de battage ;
- une rondelle métallique « martyr » (consommable) sur le casque de battage ;
- le casque de battage de 63 mm de diamètre intérieur, muni d’une goulotte d’évacuation du fluide de forage ;
- un ensemble de tiges-allonges de 122 mm de long en diamètre 32 mm, et manchons de roto-percussion, équipement classique qui doit néanmoins être robuste face à la roto-percussion ;
- un ensemble de tubes de 63 mm de diamètre extérieur et 49 mm intérieur, en éléments de 122 mm de long, vissés sans débord avec un pas étudié pour bien se comporter sous la vibration des marteaux de roto-percussion ;
- un tube fendu de 63 mm de diamètre extérieur et 49 mm intérieur mis en pied de l’ensemble tubes-tiges, muni à sa base d’un sabot ouvert et d’une réservation de positionnement de la sonde ;
- un outil destructif en roto-percussion guidé par le sabot de tubage, « extensible » au diamètre de forage et rétractable dans le tubage ; il s’agit d’un perfectionnement des outils de type Odex® rétractables connus dans des diamètres supérieurs, son diamètre étant calibré de façon à réaliser un forage ajusté à celui du tubage employé ; - un système de préhension du tubage au-dessus des vérins, constitué soit par un collier auto-serrant, soit par une enclume hydraulique annulaire ;
- un système de relevage du tubage par vérinage hydraulique vers le haut ;
- une sonde pressiométrique de type AX de 46 mm de diamètre extérieur, munie d’une pointe spéciale à ailettes mobiles permettant avec précision son positionnement au milieu de la section fendue du tube et son retrait en fin d’essais ;
- enfin le contrôleur pression-volume pressiométrique, de préférence à enregistrement des lectures sur support électronique.
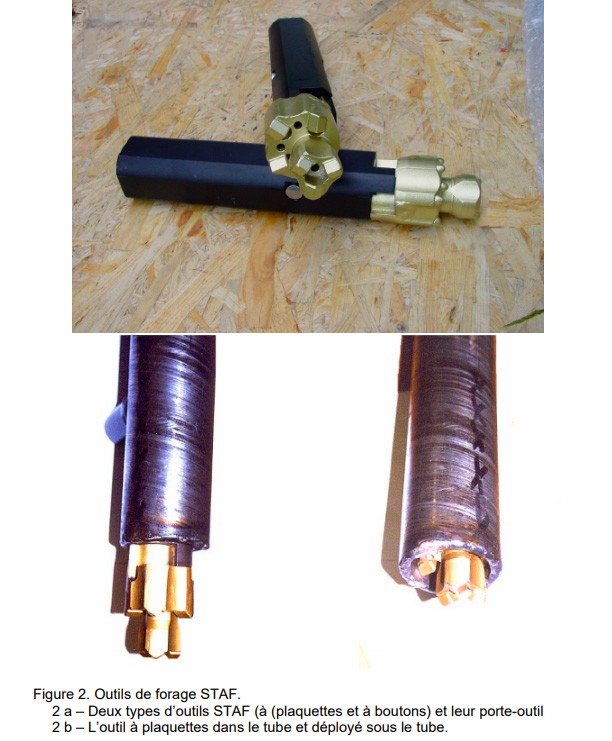
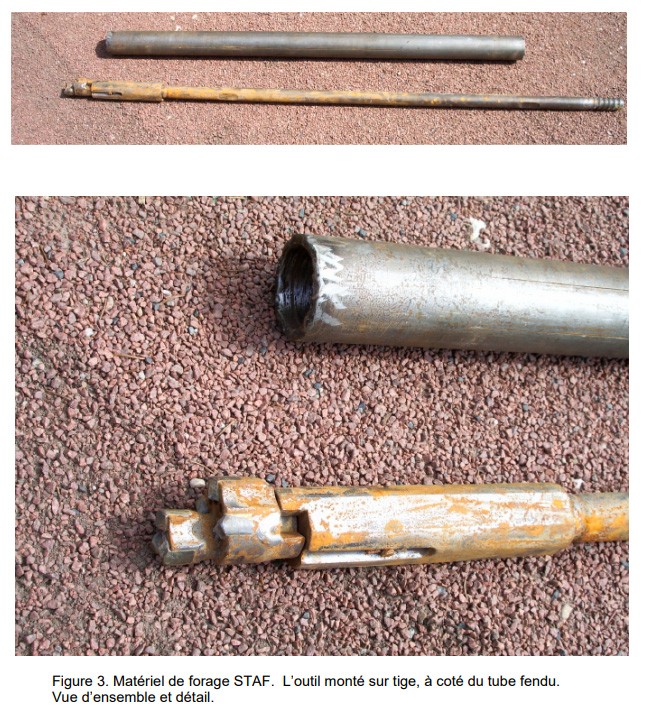
Le fonctionnement
La séquence de fonctionnement de cet ensemble est décrite par le schéma de la Figure 2. Le train de tubage descend à la même vitesse que l’outil de forage réalisant un véritable autoforage du tube fendu, lequel forme l’enveloppe protectrice et dilatable de la sonde qui sera positionnée ensuite à son niveau. L’auto-forage du tubage est caractérisé par le fait que l’outil destructif « extensible » dépasse la base du tubage et par surcroît occupe tout le maître-couple du tube. S’il y a là une entorse au principe d’auto-forage strict du tube, ce défaut est largement compensé par la possibilité de forer en continu sans changement d’outil dans tous les types de sols, depuis les sols fins compressibles jusqu’aux sols raides, caillouteux et même directement dans le rocher ou des alternances de sols et de roches cimentées. Il s’ensuit donc bien un remaniement normalisé réduit au minimum représenté par la possible décompression du terrain pendant la seconde ou la fraction de seconde entre le découpage par l’outil protubérant et l’arrivée du tubage. Une attention particulière est portée dans ce système à l’évacuation des déblais de forage, qui sont poussés vers l’intérieur du tubage par la forme de l’outil lui-même et par la direction donnée aux buses d’injection, qui n’attaquent le terrain que frontalement et favorisent la remontée du fluide chargé dans le sabot de tubage où ils sont broyés à une granulométrie suffisamment fine pour rendre plus aisée cette remontée. Le fluide de circulation, qui peut être à base de bentonite, classique mais de moins en moins employée en pratique par des ateliers de forage restant trop peu de temps sur un site de forage pour préparer une boue bentonitique suffisamment gonflée, peut aussi être une boue aux polymères à préparation quasi-instantanée. L’avantage est qu’on ne demande pas alors à cette boue à base de polymères de tapisser les parois du forage, avec laquelle elle n’est pratiquement pas en contact sauf entre l’outil de forage et le sabot de tubage, mais principalement de présenter la viscosité nécessaire pour enrober les sédiments et les remonter intégralement. L’intégralité de la boue peut être recueillie dans la goulotte à la sortie du casque de battage, ce qui permet d’une part au chef-sondeur de visualiser sa sortie continue et régulière, d’autre part de la faire immédiatement sédimenter avec la possibilité de prélever à chaque passe une partie des déblais de forage qui peuvent être mis en sachets pour une coupe sur déblais, de façon très propre. Le chantier de forage aux abords du trou reste également très propre, et la décantation dans un bac approprié (ou une double décantation) permet de rejeter un liquide de forage sans sédiments. En fin de forage, le volume du précipité de sédiments broyés dans le bas du tube est relativement concentré, et peut être utilisé, avec adjonction éventuelle d’un faible pourcentage de ciment pour la fabrication d’un coulis à réinjecter pour boucher le trou de forage, garantissant à la fois un chantier sans déchets, et le rebouchage étanche du trou de forage.
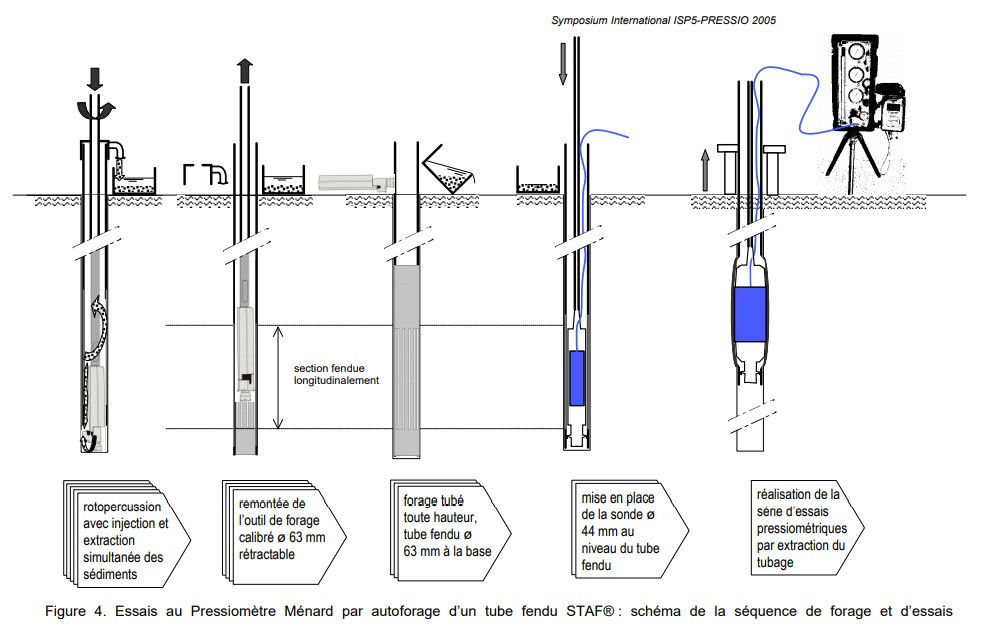
Présentation de quelques résultats d’essais
Nous allons présenter des résultats d’essais au tube fendu ouvert et au tube fendu auto-foré STAF®. Nous analyserons les qualités propres à la méthode et comparerons les résultats pressiométriques avec d’autres méthodes de forage.
Mise au point
La première mise au point de l’outil de forage excentrique rétractable de 63 mm a été faite de 2000 à 2003 et les premiers forages avec cet outil en 2003. Les premiers forages ont été tentés dans différents sols pour vérifier les difficultés de descente et de remontée du tube en fonction du diamètre de l’outil. Il s’est avéré qu’un outil débordant de quelques millimètres le diamètre du tube permettait une descente rapide et facile du train de tubage, mais conduisait à des essais avec un volume de contact trop élevé et perturbé, parce qu’en raison de cet espace annulaire même minime les déblais avaient tendance à remonter et former un bouchon autour du tube fendu. Les essais de Bruyères le Châtel, forage FP3 du projet Teratec, avec un outil à boutons balistiques illustrent ce problème : les essais sont interprétables, mais le rapport E/Pl semble surestimé en comparaison d’essais voisins en forage préalable à la boue, qui d’ailleurs ne représentent peut-être pas non plus le « vrai » module pressiométrique du terrain qui est probablement intermédiaire. L’obtention d’essais conformes aux attentes de la méthode est venue assez vite en observant les dispositions suivantes :
- utilisation d’un outil à plaquettes de tungstène de diamètre 65mm
- pression d’injection modérée ne dépassant pas 2 MPa en moyenne
- débit d’injection modéré également de 30 à 60 l/mn
- fréquence de percussion assez basse : en fait la fréquence de percussion, variable en fonction du type de choc qui diffère selon les modèles de marteau, est l’élément que le foreur peut moduler en fonction du terrain : quelques rares coups (moins de 30 coups/mn) en terrains compressibles et jusqu’à des pressions limites de l’ordre de 1 MPa, où la descente de l’ensemble tube-tiges est rapide ; augmentation de la fréquence jusqu’à 60 à 100 coups/mn en terrain moyen à raide, jusqu’à PLM de 2 à 3 MPa ; au-delà, on entre dans des terrains raides à très raides, où il faut augmenter la fréquence qui peut atteindre 300 à 500 coups/mn selon le type de percuteur, et la poussée sur l’outil pour garder une vitesse de pénétration suffisante ;
- la surveillance du débit de remontée du fluide de forage chargé de déblais est essentielle pour le foreur, toute tendance à la baisse de débit correspond à un risque de « bouchon » qu’il faut compenser aussitôt par une augmentation maîtrisée du débit d’injection, qui remet en mouvement ascendant le fluide ;
Le forage réalisé dans ces conditions réalise assez bien le travail recherché d’un trou parfaitement cylindrique et vertical : l’outil de forage bien guidé réalise complètement la destruction du terrain, et le bord rigide du sabot de tubage vient écrêter, araser la paroi au cas où il reste des fragments de sol, en se mettant en place avec un certain frottement correspondant à l’ajustement au diamètre du trou. L’extraction est relativement difficile, à partir d’une certaine profondeur : elle dépasse en général la force de traction des foreuses géotechniques courantes et nécessite l’emploi d’un système d’extraction par vérinage. Ceci, avec l’absence de remontées autour du tubage, assure que le but d’ajustement parfait du terrain autour du tubage a été atteint, sans décompression mais également sans risque de refoulement. Du point de vue de l’organisation du travail, nous avons employé soit le système bien connu de vérins sur enclume annulaire repris et adapté de la foreuse D9000 Ménard pour l’extraction du tube fendu « direct », soit un vérin annulaire actionné par l’atelier de forage. Mais il est tout à fait possible, et c’est un des avantages de la méthode, de répartir le travail entre un atelier d’autoforage du tube fendu laissant en place son train de tubages avant de se déplacer, et un atelier de pressiométrie réalisant, immédiatement derrière ou avec un décalage de temps imposé par les circonstances de chantier (voiries en circulation avec interruption limitée, par exemple), l’extraction du tubage et l’enregistrement des essais pendant la remontée.
Exemples dans différents types de sol
On trouvera dans les courbes d’essais ci-après différents types de sols et de valeurs de modules et pressions limites. A part les essais d’Avrainville, essais de mise au point et de Merville, site expérimental LCPC, il s’agit d’essais de chantiers réels, missions G0 suivies de missions G1 et ultérieures.
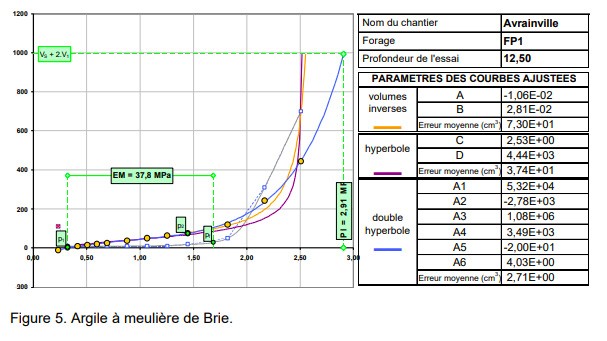
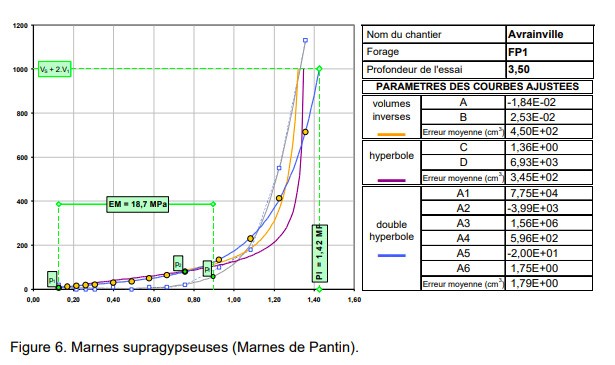
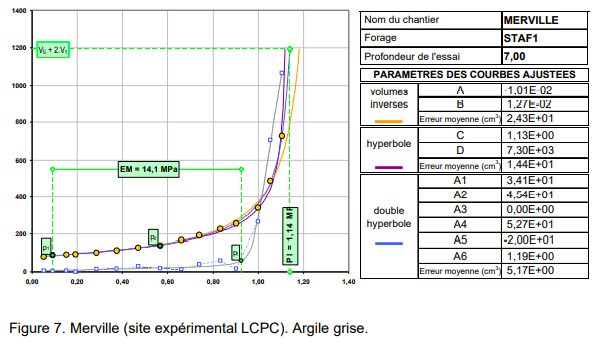
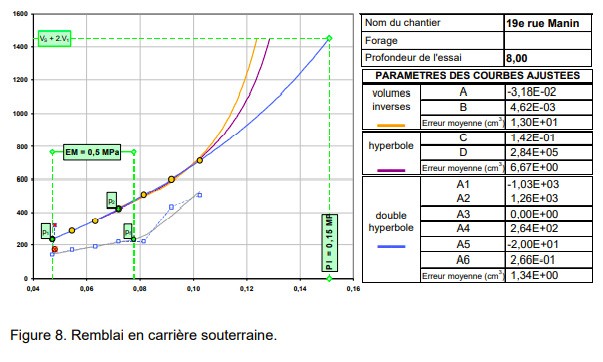
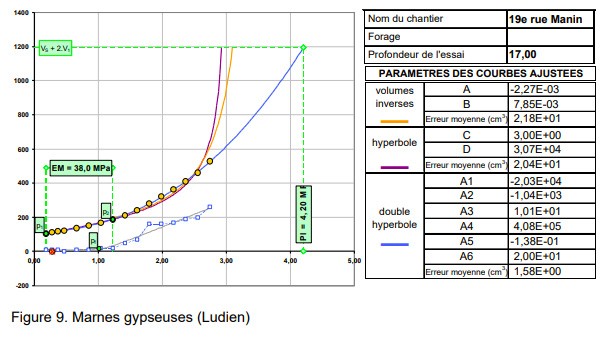
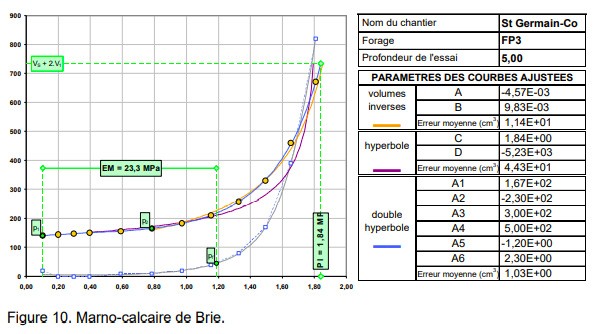
Comparaison avec des essais à forage préalable sans tubage
La campagne de forages de Villeneuve-le-Roi est particulièrement intéressante, parce qu’il s’agit de 3 forages de 15 à18 m pour la construction d’un entrepôt (sur pieux) dans un site où un précédent entrepôt (société Paprec) et une presse d’emboutissage ont été construits à proximité sur des campagnes pressiométriques avec forage préalable. La comparaison des résultats (figure 13) montre que dans les remblais et alluvions récentes de ce site, jusqu’à 11 m environ, la répartition des valeurs de EM et pLM des essais, si elle diffère dans le détail, est statistiquement peu différente. Par contre, dans le substratum marneux à marno-calcaire, les essais au STAF montrent, pour une pression limite comparable, des rapports EM/pLM mieux groupés et plus élevés ; dans le cas présent, il est certain que ces valeurs de modules sont plus proches de la réalité du terrain, et que les valeurs antérieures en forage préalable avaient légèrement sous-estimé les modules.
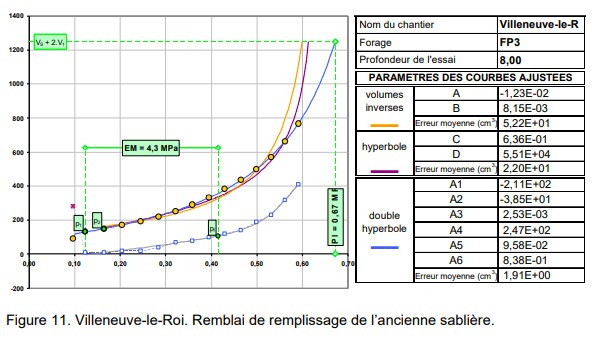
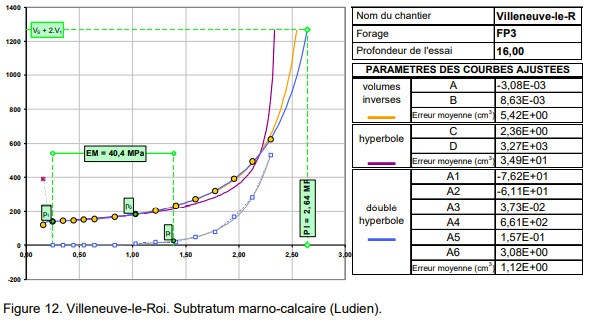
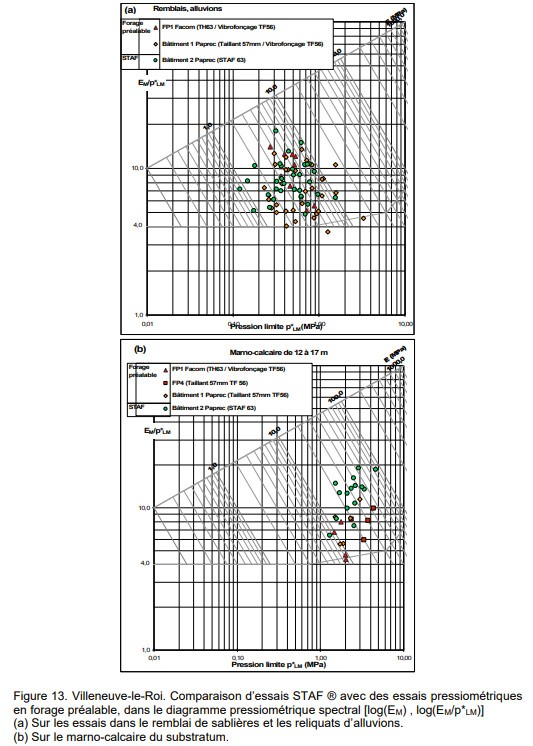
Conclusions et perspectives
Les essais présentés ci-dessus correspondent, après une période de mise au point, à une quinzaine de chantiers en vraie grandeur, à différentes profondeurs jusqu’à 22 m à l’heure actuelle ; des forages de 45 m sont prévus. Les résultats sont suffisamment encourageants pour qu’on ait déjà la certitude que l’influence du forage sur la phase initiale de l’essai est fortement atténuée. La mise au point des outils de forage et de vibro-battage se poursuit dans l’objectif de permettre la réalisation d’essais à remaniement initial négligeable dans tous types de sols.